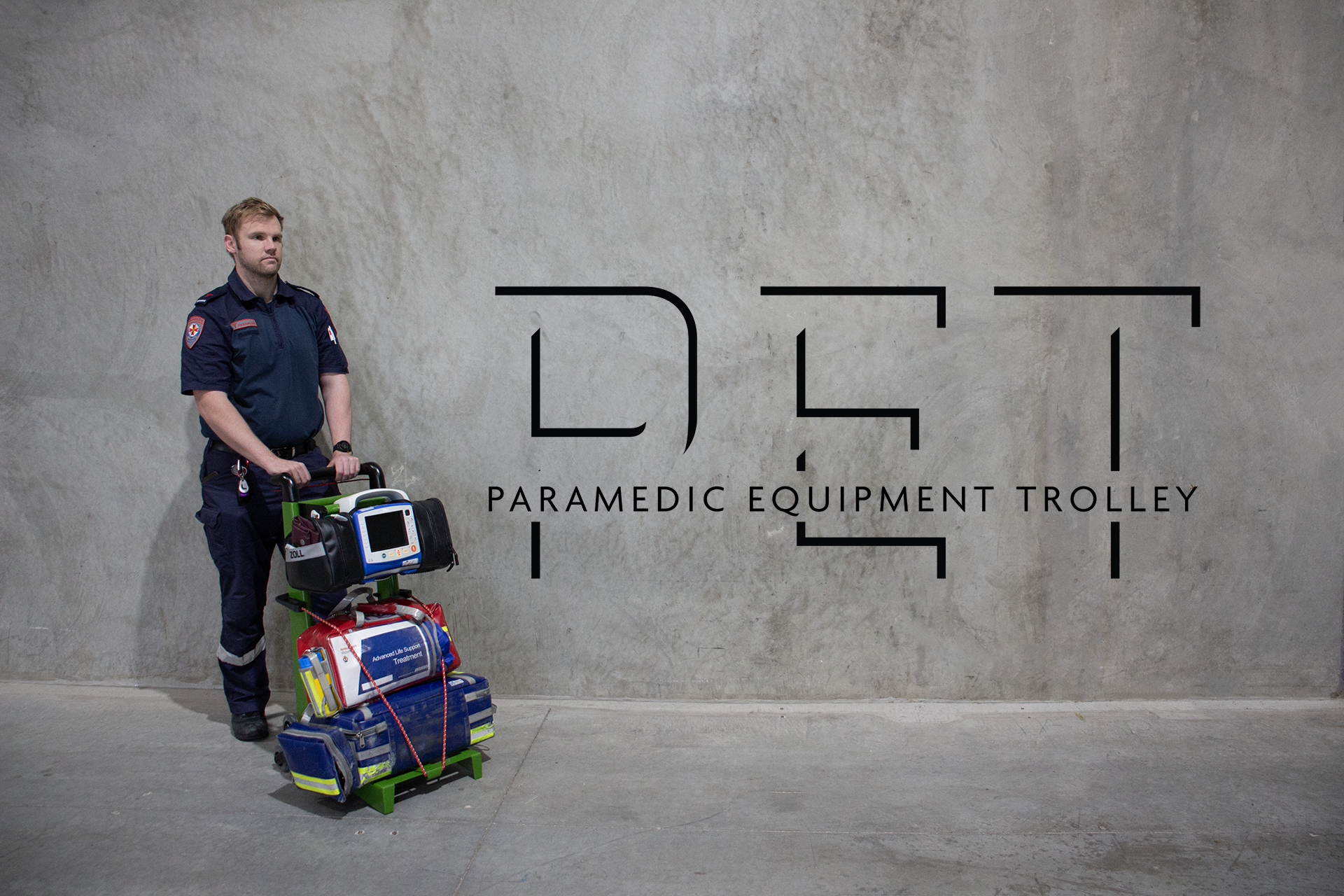
Awarded “Most outstanding Industrial Design Project”
Paramedics have one of the highest injury rates in Australia, the largest category of causes being muscular stress, mostly due to lifting and carrying.
So how might we design ergonomic interventions to reduce repetitive stress injuries among paramedics?
I explored different concepts looking at a variety of ways to solve the problem space. I developed unique solutions that focused on functionality and ease of use. This process helped inform the final concept.
Ideation
Refining
The Paramedic Equipment Trolley, P.E.T, is designed to minimise repetitive stress injuries for paramedics by offering an alternative method for transporting equipment. It integrates seamlessly into the ambulance’s existing bag tower with a hydraulic lever to assist with loading and unloading. The P.E.T includes an adjustable handlebar to accommodate various heights and an adjustable monitor hook to ensure the screen is visible from any working position. Additionally, it is equipped with “tri-wheels,” or stair-climbing wheels, making it easy to manoeuvre in any home environment.
Prototyping
Dual handles
Monitor hook with back support
Adjustable handlebar (stroller inspired)
Monitor hook
Height adjustable handle
Monitor shelf
Trolley with shelf
Dual handle with height adjustable monitor hook
PVC pipe prototype with adjustable handlebar and adjustable monitor hook. The paramedic is demonstrating how they would adjust the monitor hook in adherence to the manual handling guidelines.
Design for manufacturing
The trolley will be manufactured by laser cutting and bending a 3mm thick aluminum sheet, consisting of only three pieces for the body. Once the pieces are shaped, the frame will be welded together, resulting in a solid and sturdy trolley body.
I could not get the prototype made externally due to the time frame; however, I received confirmation that the trolley was manufacturable. I acquired sheet metal and had to adjust the drawings and production plan to align with the capabilities of the workshops at campus (WAM & Dfab). In production the trolley would have a powder coated finish, but the prototype is spraypainted.
Prototype
The trolley prototype features a robust structure crafted from aluminium sheets, ensuring durability and lightweight functionality. The handle, designed for comfort and ease of use, along with the occy hooks, was produced using 3D printing.